Transforming Industries with **Electrical Plastic Molding**
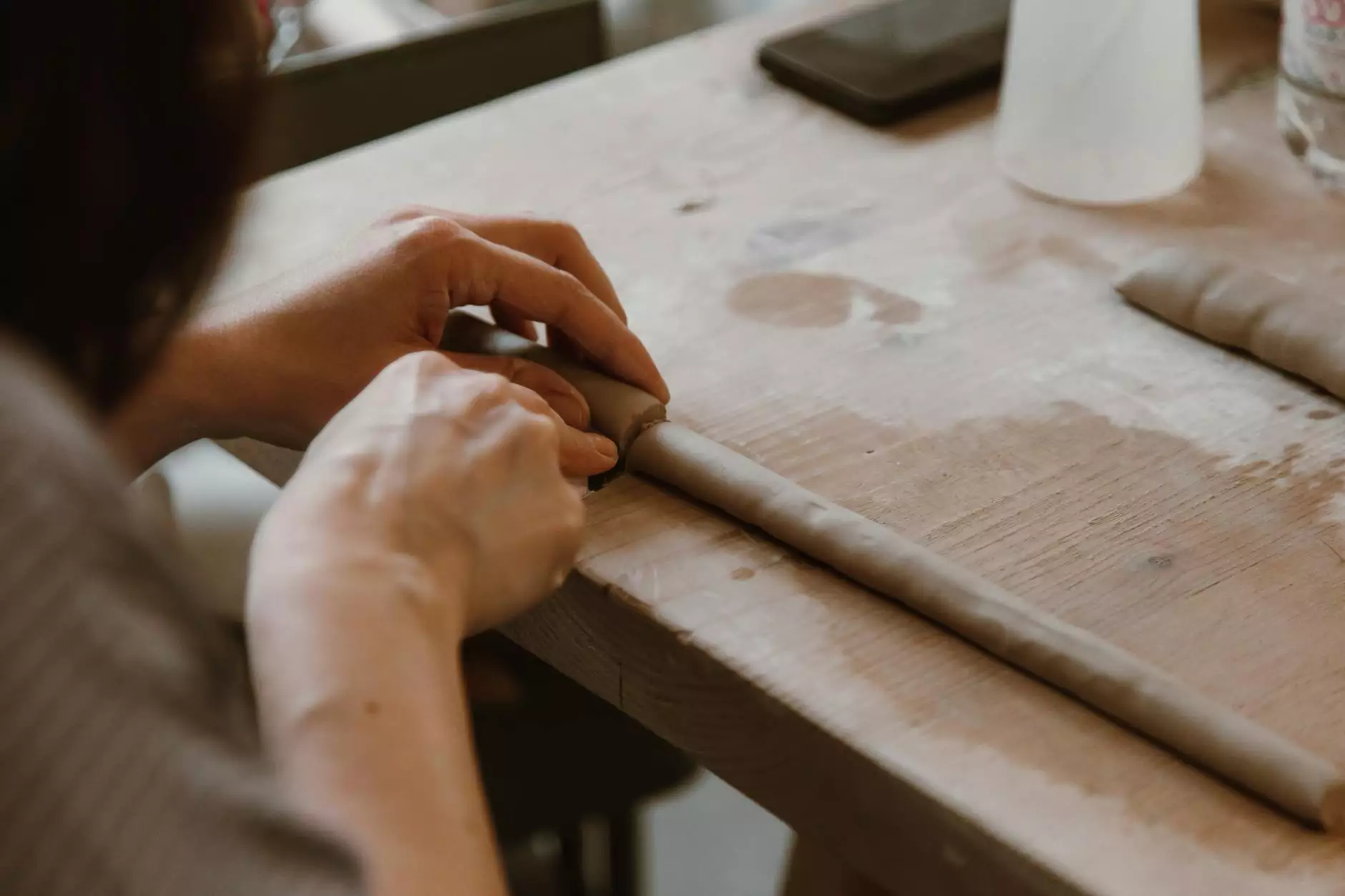
In today's fast-paced industrial environment, the demand for quality and efficiency is at an all-time high. This is particularly true in the realms of manufacturing and design, where Electrical Plastic Molding stands as a pivotal process. At DeepMould, we specialize in delivering high-end molding solutions that cater to a variety of industry needs, particularly focusing on the category of Metal Fabricators.
Understanding Electrical Plastic Molding
Electrical Plastic Molding refers to the process of creating plastic parts through the injection of molten plastic into molds that shape the desired product. This method is especially crucial in the fabrication of electrical components, where precision and durability are of utmost importance.
The Importance of Electrical Plastic Molding in Modern Industry
The role of Electrical Plastic Molding has become increasingly significant in a variety of sectors. Here are some of the key reasons why:
- Cost-Effectiveness: Compared to traditional manufacturing techniques, plastic molding can save time and reduce material waste, leading to lower production costs.
- Design Flexibility: Molding allows for intricate designs that would be challenging or impossible to achieve with other methods.
- Material Variety: A wide array of plastics can be used, offering options for durability, flexibility, and thermal resistance.
- Repeatability: Once a mold is created, thousands or even millions of identical parts can be produced with remarkable consistency.
Exploring the Process of Electrical Plastic Molding
The Electrical Plastic Molding process encompasses several crucial steps, all of which contribute to the final product's quality and functionality:
1. Material Selection
The first step is selecting the appropriate type of plastic. Factors such as thermal conductivity, insulation properties, and strength determine the choice of material. Common plastics used include:
- Polycarbonate (PC)
- Polypropylene (PP)
- Acrylonitrile Butadiene Styrene (ABS)
- Nylon (PA)
2. Mold Design
The next critical aspect is designing the mold itself. Computer-aided design (CAD) software is often employed to create precise mold specifications that meet the specifications of the electrical components being produced. At DeepMould, we utilize state-of-the-art technology to ensure impeccable mold designs.
3. Injection Molding
Once the mold is created, the chosen plastic material is heated until it becomes liquid and then injected into the mold under high pressure. This step is crucial as it determines the final shape and texture of the product.
4. Cooling and Solidification
After injection, the material is allowed to cool and harden. This stage is integral to forming a solid product that maintains precise dimensions.
5. Quality Control
At DeepMould, we prioritize quality control. Our team inspects each batch of molded products meticulously to ensure they meet the specified standards. This may include electrical testing, dimensional checks, and visual inspections.
Applications of Electrical Plastic Molding in Various Industries
The versatility of Electrical Plastic Molding has enabled its application across multiple sectors. Here are a few notable fields where it plays a vital role:
1. Automotive Industry
In the automotive sector, molded plastics are used for various components, including dashboard components, connectors, and switches. The durability and lightweight nature of plastics enhance vehicle performance by improving fuel efficiency.
2. Consumer Electronics
Devices such as smartphones, laptops, and household appliances rely heavily on precisely molded plastic components. This ensures they function efficiently and safely, particularly in electrical conduction and insulation.
3. Electrical and Electronics
From circuit breakers to connectors, components made through Electrical Plastic Molding meet strict safety and performance standards, ensuring reliable operation in critical situations.
4. Medical Devices
In the healthcare industry, molded plastics are essential for creating components such as housings for medical electronics, ensuring they are lightweight and durable while maintaining sterilization standards.
Advantages of Choosing DeepMould for Electrical Plastic Molding
When it comes to Electrical Plastic Molding, choosing the right partner is critical for achieving high-quality results. Here’s why DeepMould stands out:
- Expertise: Our team comprises experienced professionals who understand the nuances of plastic molding and manufacturing processes.
- Advanced Technology: We leverage cutting-edge technology for mold making and production, ensuring high levels of precision and efficiency.
- Custom Solutions: We offer tailored solutions to meet the specific needs of our clients, ensuring their projects are successful from concept to completion.
- Commitment to Quality: Our stringent quality control measures guarantee that every product meets or exceeds industry standards.
- Sustainability: We are committed to sustainable practices, minimizing waste and employing recyclable materials whenever possible.
Future Trends in Electrical Plastic Molding
The landscape of Electrical Plastic Molding is continuously evolving, influenced by advancements in technology and changing consumer demands. Here are some trends to watch:
1. Automation and Smart Manufacturing
The integration of automation in the molding process enhances efficiency and reduces human error. Smart manufacturing techniques, including IoT applications, are gradually being adopted to streamline production and monitoring.
2. Biodegradable Plastics
As environmental concerns grow, the demand for biodegradable plastics is increasing. Manufacturers are exploring innovative materials that provide the same functionality as traditional plastics while being kinder to the planet.
3. Enhanced Design Software
Advancements in CAD and simulation software allow for greater design flexibility and quicker prototyping. This results in the ability to test and refine designs in a fraction of the time.
Conclusion
Electrical Plastic Molding is a cornerstone of modern manufacturing, offering a host of benefits that drive innovation in various sectors. At DeepMould, we are dedicated to providing exceptional molding services anchored in quality, precision, and sustainability. Whether in automotive, medical, or consumer electronics industries, our commitment to excellence makes us a leader in the field. As we move toward an increasingly automated and eco-conscious future, we are excited to continue pushing the boundaries of what is possible in Electrical Plastic Molding.